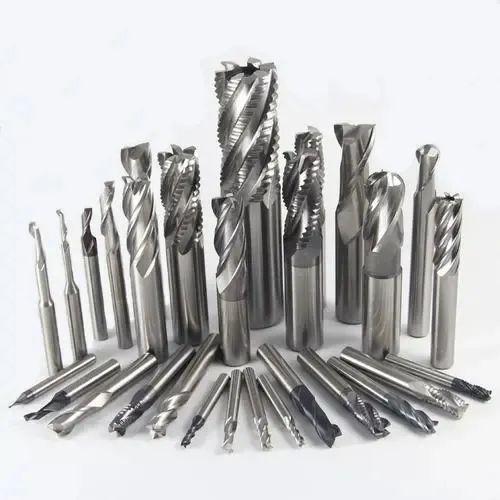
Модерни материјали за резне алате искусили су више од 100 година историје развоја од угљеничног алатног челика до брзог алатног челика,цементирани карбид, керамички алатисупертврди материјали за алат.У другој половини 18. века првобитни материјал алата био је углавном угљенични алатни челик.Зато што је у то време коришћен као најтврђи материјал који се могао машински обрађивати у резним алатима.Међутим, због своје веома ниске температуре отпорне на топлоту (испод 200°Ц), угљенични алатни челици имају недостатак што су одмах и потпуно тупи због топлоте резања при резању при великим брзинама, а опсег резања је ограничен.Стога се радујемо материјалима за алате који се могу резати великом брзином.Материјал који се појављује да одражава ово очекивање је брзорезни челик.
Брзорезни челик, познат и као предњи челик, развили су амерички научници 1898. Није толико да садржи мање угљеника од угљеничног алатног челика, већ је додат волфрам.Због улоге тврдог волфрамовог карбида, његова тврдоћа се не смањује у условима високе температуре, а пошто се може резати брзином много већом од брзине резања угљеничног алатног челика, назива се брзорезним челиком.Од 1900~-1920, појавио се брзорезни челик са ванадијем и кобалтом, а његова топлотна отпорност је повећана на 500~600 °Ц.Брзина резања челика достиже 30~40м/мин, што се повећава за скоро 6 пута.Од тада, серијализацијом његових саставних елемената, формирани су брзорезни челици од волфрама и молибдена.До сада је у широкој употреби.Појава брзорезног челика изазвала је а
револуција у обради сечења, значајно побољшавајући продуктивност сечења метала и захтевајући потпуну промену структуре алатне машине како би се прилагодила захтевима перформанси резања овог новог материјала алата.Појава и даљи развој нових машина алатки је заузврат довела до развоја квалитетнијих алатних материјала, а алати су стимулисани и развијени.У условима нове технологије производње, алати од брзорезног челика такође имају проблем ограничавања трајности алата због топлоте резања при резању великом брзином.Када брзина сечења достигне 700 °Ц, брзорезни челик
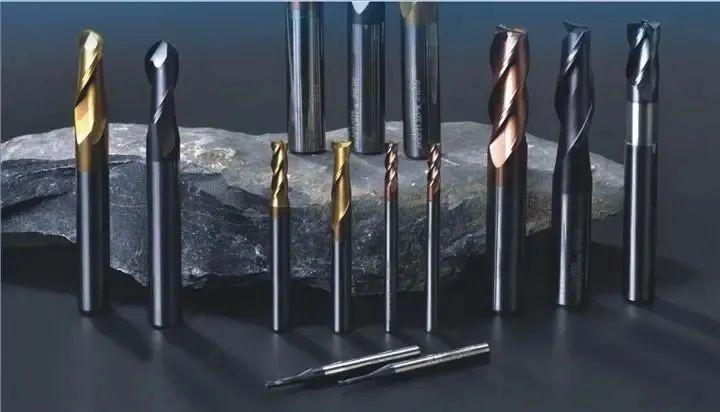
врх је потпуно туп, а при брзини сечења изнад ове вредности, потпуно је немогуће сећи.Као резултат тога, појавили су се карбидни материјали алата који одржавају довољну тврдоћу у условима виших температура резања од горе наведених и могу се сећи на вишим температурама резања.
Меки материјали се могу сећи тврдим материјалима, а да би се секли тврди материјали потребно је користити материјале који су тврђи од њега.Најчвршћа супстанца на Земљи у овом тренутку је дијамант.Иако су природни дијаманти одавно откривени у природи и имају дугу историју употребе као алата за сечење, синтетички дијаманти су такође успешно синтетизовани још раних 50-их година 20. века, али права употреба дијаманата за широку производњуматеријали индустријског резног алатаје и даље питање последњих деценија.
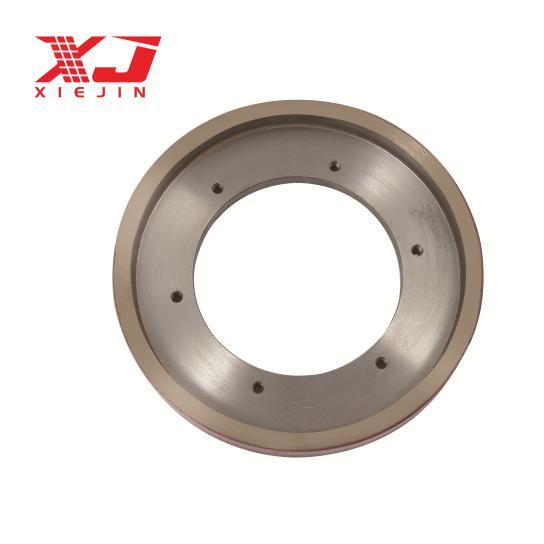
С једне стране, развојем савремене свемирске и ваздухопловне технологије, употреба савремених инжењерских материјала постаје све обилнија, иако су побољшани брзорезни челик, цементирани карбид инови керамички материјали за алату резању традиционалних обрадака, брзина резања и продуктивност сечења су се удвостручили или чак десетине пута повећали, али када се користе за обраду горе наведених материјала, издржљивост алата и ефикасност резања је и даље веома ниска, а квалитет сечења је отежан да гарантује, понекад чак и неспособну за обраду, потребу за коришћењем оштријих и отпорнијих на хабање материјала алата.
С друге стране, брзим развојем модернепроизводња машинаи прерађивачка индустрија, широка примена аутоматских машина алатки, компјутерске нумеричке контроле (ЦНЦ) обрадних центара и беспилотних машинских радионица, како би се додатно побољшала тачност обраде, смањило време промене алата и побољшала ефикасност обраде, све су хитнији захтеви. направљен да има издржљивије и стабилније материјале за алат.У овом случају, дијамантски алати су се брзо развијали, а истовремено и развојматеријали дијамантског алататакође је у великој мери промовисан.
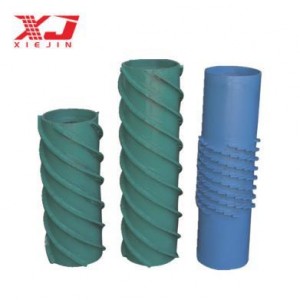
Материјали за дијамантски алатимају низ одличних својстава, са високом прецизношћу обраде, великом брзином сечења и дугим веком трајања.На пример, употреба Цомпак (поликристални дијамантски композитни лим) алата може да обезбеди обраду десетина хиљада делова клипних прстена од легуре силицијум алуминијума и њихови врхови алата су у основи непромењени;Алуминијумске летве за машинску обраду са Цомпак глодалима великог пречника могу постићи брзину сечења до 3660м/мин;Они су неупоредиви са карбидним алатима.
Не само то, употребаматеријали дијамантског алататакође може проширити поље обраде и променити традиционалну технологију обраде.У прошлости је обрада огледала могла да користи само процес брушења и полирања, али сада не само природни монокристални дијамантски алати, већ се у неким случајевима могу користити и ПДЦ супер-тврди композитни алати за супер-прецизно блиско сечење, како би се постигло окретање уместо млевења.Уз примену одсупер-тврди алати, појавили су се неки нови концепти у области машинске обраде, као што је употреба ПДЦ алата, ограничавајућа брзина окретања више није алат већ машина алатка, а када брзина окретања пређе одређену брзину, радни предмет и алат не топлота.Импликације ових револуционарних концепата су дубоке и нуде неограничене изгледе за модерну машинску индустрију.
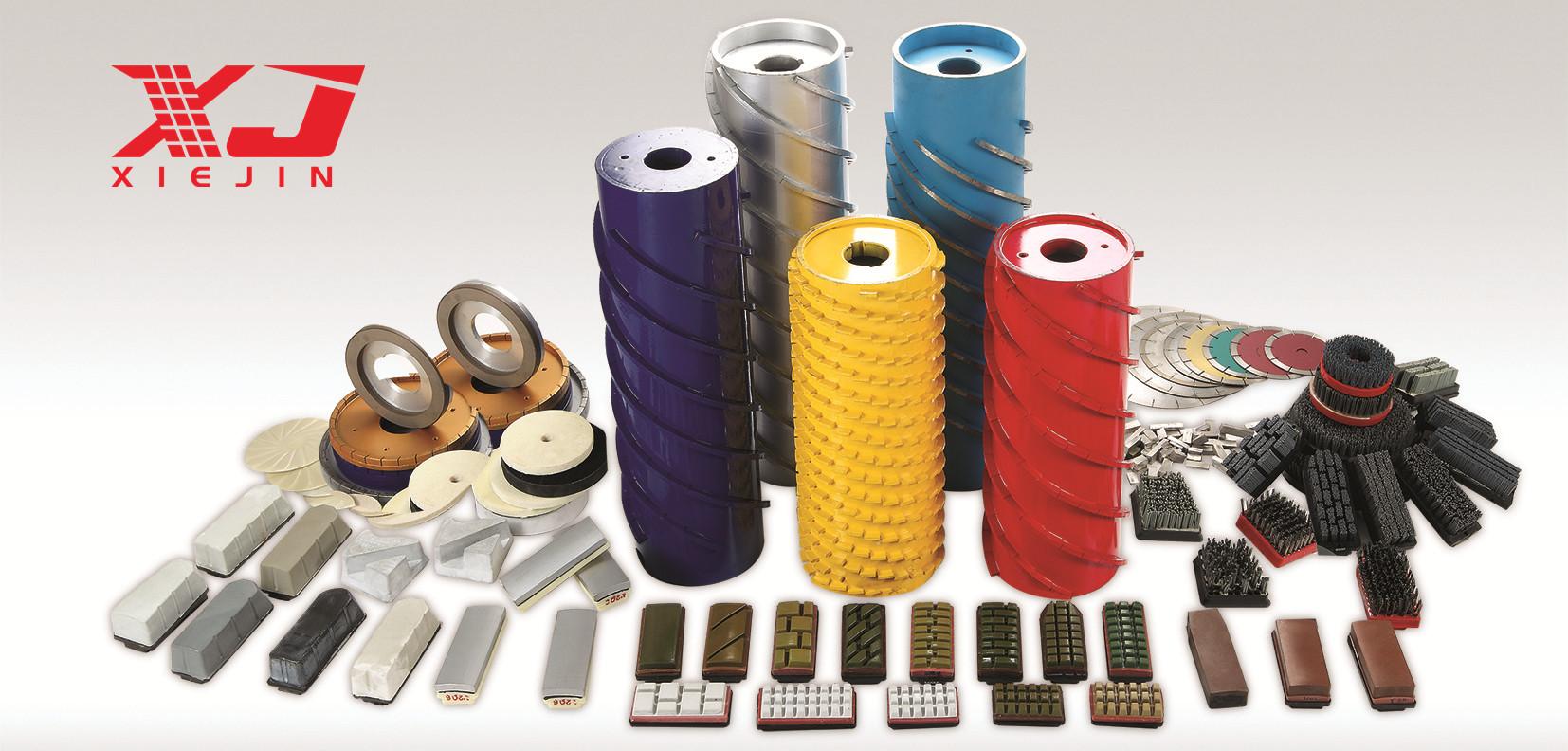
Време поста: 02.11.2022